3D Printing for Implantable Medical Devices
3D Printing Approaches Overview:
3D printing (additive manufacturing) processes produce three-dimensional parts through addition of material in a layer by layer fashion. Resorbable materials may be 3D printed using a variety of approaches including fused filament fabrication (FFF), selective laser sintering (SLS), and resin-based methods such as stereolithography (SLA) and dynamic light processing (DLP).
FFF produces parts by melting a continuous thermoplastic filament via extrusion through a heated printer head. Although the most widely utilized 3D printing technology, FFF also exhibits the lowest resolution with most printers requiring minimum layers heights ~100 microns and maximum XY resolution ~250 microns. SLS creates parts by sintering powdered materials with a laser to near-melting temperatures which causes the powder particles to fuse together to form a solid structure. SLS exhibits medium printing resolution most printers requiring minimum layer heights ~60 microns and maximum XY resolution ~80 microns. SLA produces parts through a photopolymerization process where a UV laser is focused on a photopolymer vat. SLA exhibits the highest resolution of the described methods with a minimum layer height ~50 microns and maximum XY resolution ~50 microns. Bioresorbable 3D printing materials are available for FFF, SLS, and more recently SLA-based printing methods.
3D Printing Unlocks New Design Architectures for Tissue Scaffolds:
Traditional injection molded parts are limited to solid infill designs due to the requirement resin flowing throughout a mold. In contrast, 3D printing allows for complex infill geometries such as the gyroid and honeycomb patterns to alter both the mechanical properties and cellular infiltration into the device based on its intended use. Additionally, utilization of bioresorbable materials allows for the device to maintain mechanical strength while it is needed, and to degrade into constituents that may be metabolized or excreted once the healing process has sufficiently progressed.
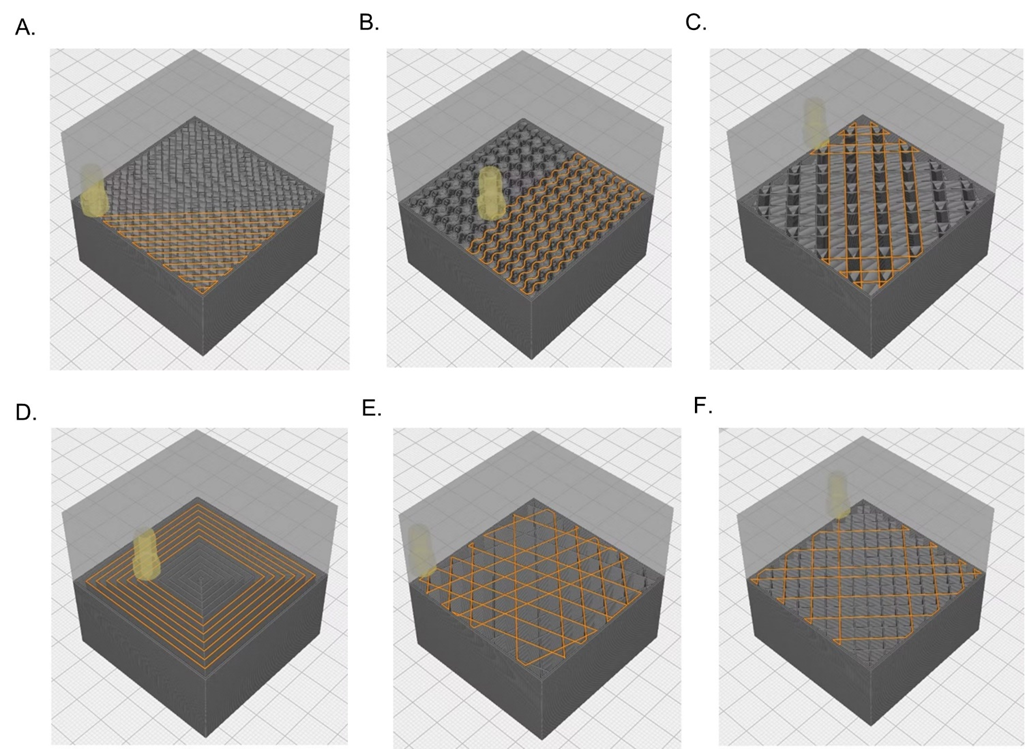
FFF 3D Printing versus Micro Injection Molding Bioresorbable Devices:
Micro-injection molding is a manufacturing process capable of producing parts between 0.1- 1 gram with tolerances ranging from 10-100 μm. As with traditional injection molding, design changes to the part mold may be prohibitively expensive with each mold costing ~$10,000 for low-volume/simple molds and up to $100,000 to high volume molds. Given the high barrier to entrance into injection molding, PMI’s FFF filament line of materials offers biomedical engineers the ability to iteratively test bioresorbable medical devices designs quickly and cost effectively. Additionally, PMI’s FFF filament materials are offered in standard 1.75 mm formats that are compatible with most open source FFF printers. For volumes applicable to many implantable medical devices, FFF printing is an economical alternative to injection that opens new design features to be imparted better suited for bioabsorbable implants.
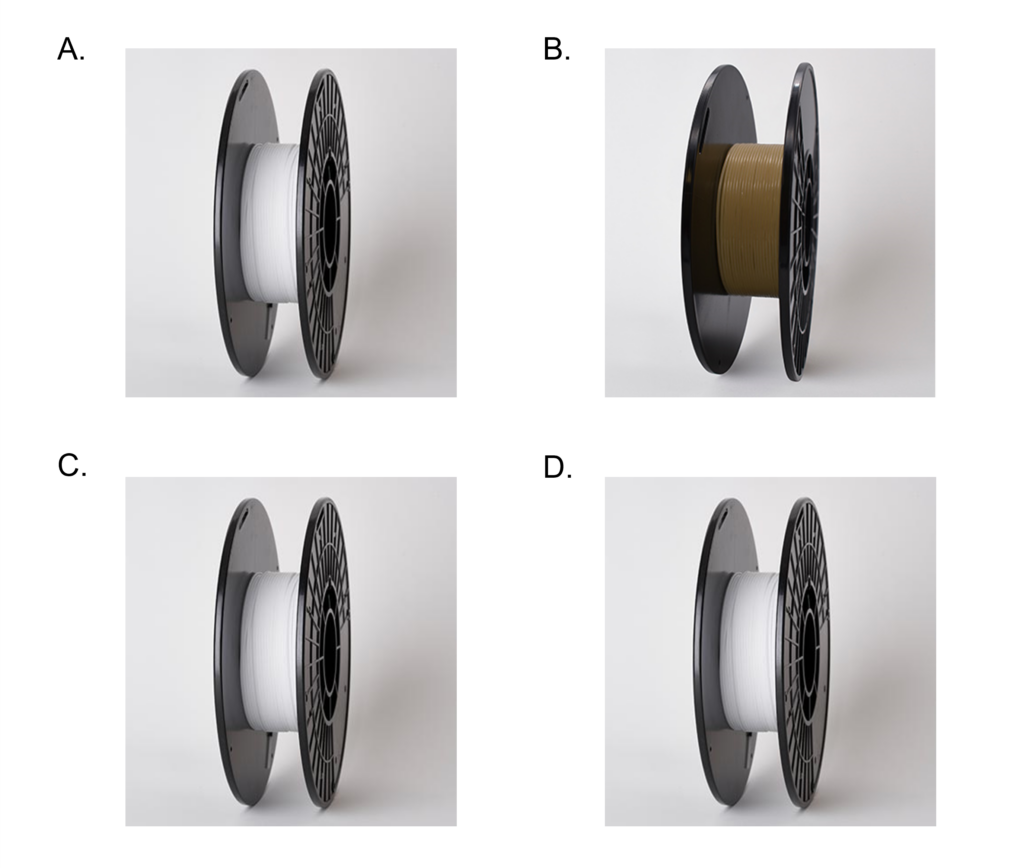
Poly-Med’s now offers Photoset® Resin for Photo-Polymerization 3D Printing Methods:
Poly-Med’s team of material scientists have developed first-in-class bioresorbable fast-degrading resins for photopolymerization 3D printing methods that include SLA, DLP, and two (2) photon polymerization. In contrast to the limited bioresorbable 3D printing resins currently available, Poly-Med’s Photoset® resin product line utilizes monomeric constituents that have used in medical devices for over forty (40) years and are anticipated to be biocompatible with the data collected to date. Additionally, Poly-Med’s material scientists can tune the Photoset® resin mechanical properties and degradation timeline to best meet a device’s requirements. 3D printing with Poly-Med’s Photoset® resin allows for unparalleled resolution when manufacturing bioresorbable medical implants that require small design features.
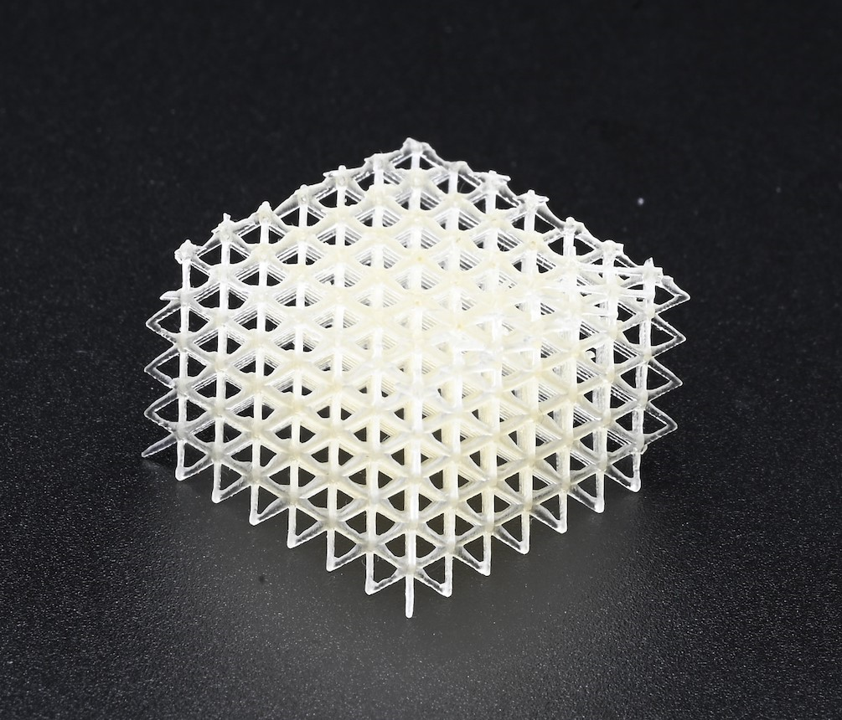
Poly-Med’s 3D Printing Services:
In addition to supplying materials, Poly-Med also offers design engineering and 3D printing services for parts made of FFF and SLA materials. Whether a design is not in its final iteration and consultation is needed or if a part design has been finalized and prototypes are needed for testing, Poly-Med’s design engineering is available to provide requested services.
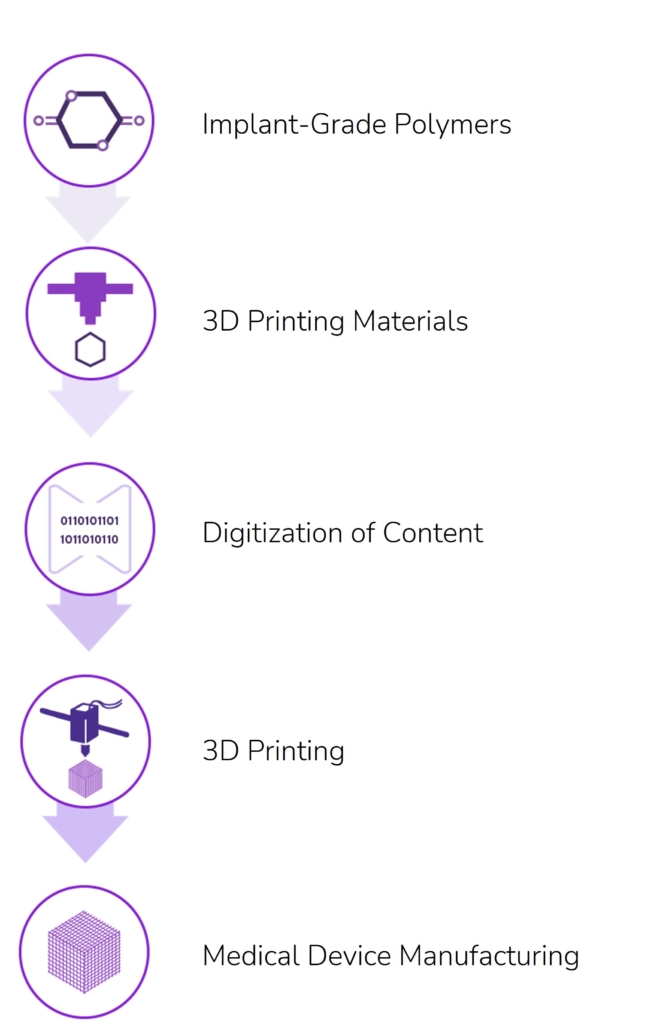
Figure 4: Poly-Med offer fully service 3D printing design, development, & manufacturing services for absorbable medical devices.
Poly-Med is a Vertically Integrated Bioresorbable Medical Device Manufacturing Partner:
Manufacturing bioabsorbable medical devices is hard. Controlling moisture levels and material degradation through the production cycle requires specialized equipment and process controls to ensure quality of finished devices. In contrast to other bioresorbable polymer manufacturers, Poly-Med produces polymer, is able to extrude this material to desired monofilament or multifilament formats, and is able process this material via warp knitting, weft knitting, or braiding processes to produce custom biomedical textiles. Beyond traditional textiles, we can process our bioresorbable polymers into non-woven formats via electrospinning via our state-of-the-art electrospinning facility. In addition to accessing Poly-Med’s more than thirty (30) years of experience manufacturing bioresorbable polymers, partnering with Poly-Med simplifies your bioresorbable medical device manufacturing supply chain. Contact us to today begin developing your custom bioresorbable medical device product line with a trusted partner for manufacturing advanced bioresorbable medical devices or purchase off-the-shelf high-performance bioresorbable polymers!
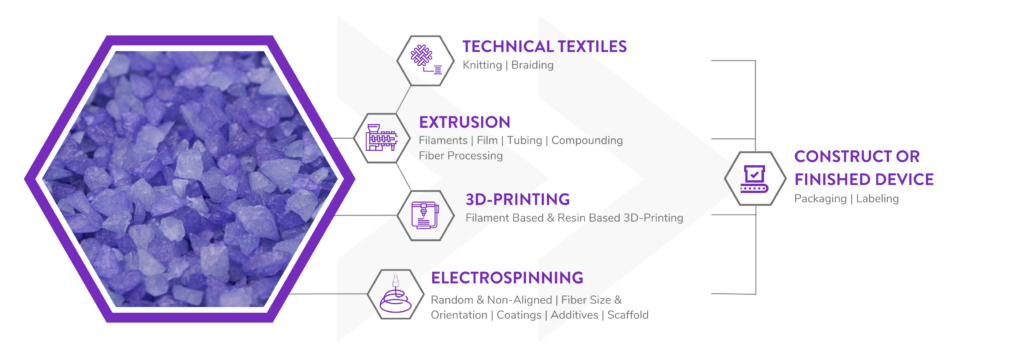